Aerospace Industry
Acres, Solutions Provider to the Aerospace Industry
You too can benefit from working with Acres, a supplier focussed on value-add and continual improvement. We understand the speed in which the industry moves and the key drivers.
Key Drivers
Acres’ offering to the aerospace industry aims to take time out of manufacturing processes and prevent parts from becoming damaged or lost.
This can be anything from kitting media to delivering the exact number of components from a logistics sequencing centre to a production build line; all the way to semi-automated product for carrying out specific operations, which are provided with a certificate of conformance (commonly referred to as a CE certificate). We specialise in the design and fabrication of equipment that is used in the manufacturing process, such as stillages, trolleys, access platforms, workbenches.
-
The quality and care of components is critical.
-
Safety & FOD control is paramount.
-
Team member engagement is key to project success.
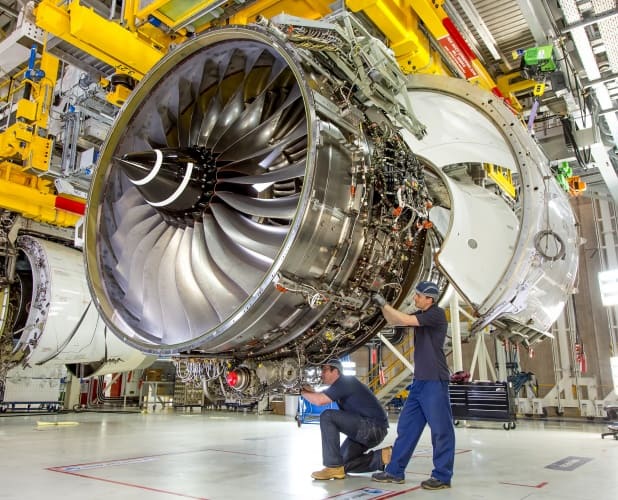
Expertise
We understand the speed in which the industry moves and some of the key drivers like safety, efficiency, quality and FOD (foreign object debris) control.
Acres lean engineering experience fits well within the aerospace environment, focusing on value-add and continual improvement. The products Acres deliver are in use across the UK’s leading aerospace manufacturing companies, improving productivity and safety of production processes, enabling them to achieve the best possible outcomes. This is further consolidated on a global basis through networking events and memberships with for example the Midlands Aerospace Alliance..
-
World class product design.
-
Kitting media, build stands, jigs & fixtures
-
Multi-sector solutions
Our Aerospace History
Situated near the Rolls-Royce plant in Derby, Acres relationship began in the 1970’s.
The relationship has enabled Acres to grow in both understanding of the industry and the wide variety of support products needed to produce finished aero engines. By their nature, aero engines require a high level of safety; and the adherence to policies and procedures is paramount to deliver world class products. The UK aerospace sector is the second largest in Europe, and third largest globally. Capable of delivering whole-aircraft capability, the UK has expertise in aerostructures, propulsion, systems, aircraft interiors and through-life services. We have a history of supporting other global aerospace clients such as GE.
-
Our origins with Rolls-Royce
-
Aerospace & Acres DNA
-
Continual Improvement
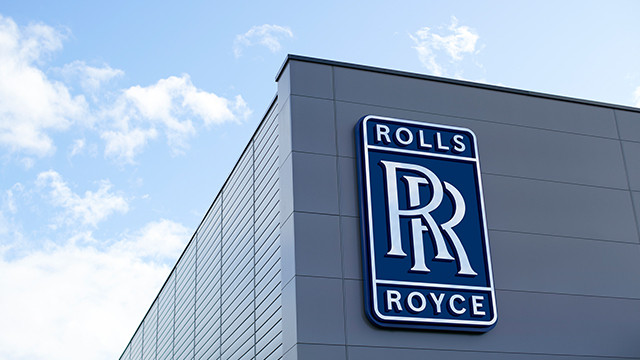
Case Study - Develop a bespoke steel cabinet from pre-determined performance criteria to provide a secure and controlled environment for castings of delicate aerospace engine parts.
A leading aerospace engine manufacturer utilise a process to manufacture 12 blade fans from high level alloys and metals. This process involves creating ceramic moulds into which the molten metals are poured and cast.
Once the metal is poured at very high temperatures, the castings are left on pallets and allowed to cool. This leaves them exposed to damage and from a Health and Safety perspective, poses a significant risk of burning personnel who may inadvertently touch or be in contact with the castings.
The client has no control over the rate of cooling of the castings and the fan mouldings, this being sublet to atmospheric conditions at the time within the factory. During this cooling period, tiny shards and fragments of the ceramic casings dislodge from the casings, adding to overall unsatisfactory process.
As a consequence, the Company was unable to determine whether or not the moulds could be safely removed from the fans. Damage is often caused to these very sensitive pieces of aerospace technology as a result of early removal.
The clients engineers provided Acres with detailed and precise measurements of a cabinet they felt could accommodate their mouldings. These included internal dimensions that had been optimally calculated from heat displacement, times and cooling rates that the casings and fans must achieve and perform to in order to provide a controlled cool down.
Acres Engineering was challenged to develop and engineer a cabinet with the capacity to hold the ceramic moulds and with the addition of as yet undetermined safety features, heat monitoring equipment and a method of containing the ceramic loosened during the cooling process.
Constrained by the footprint of the proposed cabinet and the limitations of the internal space envelope, considerable doubt and uncertainty existed in the minds of the engineers as to whether or not a fully operational cabinet was a viable proposition for the client.
The first feature that posed considerable challenges to Acres Engineering was the method of access into the cabinet. Lifting equipment was to be used to raise, insert and lower the casings so the engineers considered various options of door configurations. For optimum access a vertical door was selected for trial. This was chosen above all other options as a conventional hinge door may restrict access if not fully opened.
This methodology however stretched the development team who attempted to select an appropriate hinge with the capacity to hold the weight of the steel door and its insulation. The team trialled several options of pneumatic lift systems until they were satisfied that one was capable of holding the weight in an open position.
Uncertain of the long-term viability of the lift mechanism to maintain itself in its fully open position, Acres engineers sough to devise a safety and security feature based on an inertia reel principle found in car seatbelt mechanisms. This provided a similar action that would prevent the belt from deploying due to sudden movement of the door.
Space constrained within the cabinet envelope, engineers were challenged o develop a hopper tray to gather and collect the entire residue fallen from the casings.
The inclusion of internal electronic heat sensors with digital external read out meters for observing and monitoring the rate of cool down added to the complexity of fully developing the cabinet.
Finally after several re-engineering iterations of critical features, a fully operational prototype has been presented to the client for final approval.