Rail
Acres, Solutions Provider to the Rail Industry
You too can benefit from working with Acres, a supplier focussed on value-add and continual improvement. We understand the speed in which the industry moves and the key drivers.
Key Drivers
Rail manufacturers benefit from a supplier that delivers returnable packaging and stillaging ROI through intelligent design .
The rail industry has changed considerably in the UK in the last 10 years, and has an exciting future ahead of it with investment in infrastructure, technology and rail vehicles. Areas such as de-carbonisation, ticketing, mobility, digital and customer experience will be continually developing and evolving in the coming years. Harnessing technology and making these types of advancements drives change through products, services and processes. This is where Acres steps in. We understand that with change comes new requirements and new challenges. Our clients choose to work with us because we understand the key industry drivers such as safety, quality and return on investment (ROI). Whether you are looking to improve production efficiency, design a new product or need support with retro-fit bracketry, we’re your supplier.
-
Delivered on time - no project delays
-
Fit for purpose, safe and certified
-
Winning design and quality
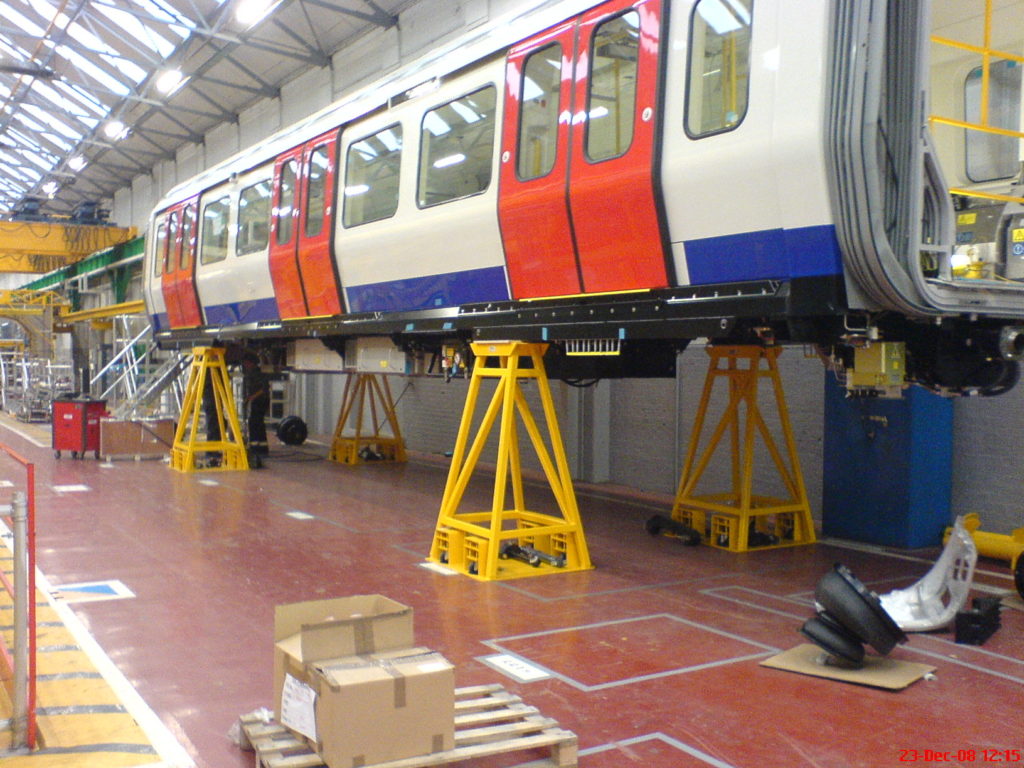
Expertise
Acres specialise in kitting media and production support equipment aimed at driving quality, health and safety, and productivity improvements.
Our expertise in design, fabrication, powder coat and mechanical-electrical assembly delivers world class products. Within the rail industry our products have typically been aimed at improving safety, productivity and efficiency. We’ve been involved in material and sub-assemblies flow, ensuring that parts are presented in an efficient and ergonomic way. We’ve also been involved in pieces of test equipment, bracketry and sub-contract fabrication. If you are looking for a supplier who is focussed on continual improvement, Acres is the supplier for you.
-
World class product design
-
Component handling, protection and presentation
-
Improving productivity performance
Expert Insight
Question and Answers with Rail Industry Insider Suly Correa, Project Contract Coordinator (Crossrail) at Bombardier Transportation.
Bombardier Transportation is a leading rail engineering and manufacturing company, headquartered at the iconic Litchurch Lane facility in Derby.
- Tell us about yourself- Who is Suly? When you aren’t working, what do you like to do to relax?
- I am a Brazilian living in UK for over 15 years and proud mum of two amazing kids. In my spare time I love exercising, travelling, baking cakes and playing piano.
- What has been your biggest achievement that you are proud of?
- Becoming a mum is the biggest achievement of my life for sure and finishing my University degree while my kids were still babies was another big achievement that I am very proud of.
- When was your first introduction to the Rail industry and why did you choose to work in the Rail industry? What drew you towards it?
- My first experience on the Rail industry was when I joined London Underground back in 2007 where I worked as Customer Service Assistant and Control Room Assistant for nearly 7 years. After a 2 years break in Brazil and a change in my career I came back in UK and joined Bombardier in 2016 as a Project Buyer working in Procurement which I love.
- Why is specification and safety so important in terms of the equipment used within the industry?
- Specification provides clear instructions on the intent and performance of the equipment and the delivery of optimal specifications to supplier can reduce health and safety hazards.
- What are you most passionate within Rail?
- I love the history of the rail in UK and the important role it has played In many crucial times like WWI and the feeling that a train journey can take you back in time sometimes is amazing.
- Have there been any new developments that you are excited about?
- I am very excited for HS2 and the development it will bring to the North of the country and will for sure open up more business and employment opportunities to many.
- What do you see as the immediate priorities for the industry are there any challenges that the Rail industry faces??
- Modernisation of fleets and routes to accommodate the number of passengers however due to Covid the prospectus may change and the demand for new trains too so the industry must adapt to what is to come from now on.
- How has the Rail industry been affected by Covid?
- The Rail industry like any other has been very affected by Covid. The number of rail journey has been dramatically reduced during 2020 and number of Passengers using the system has declined to numbers never seems before therefore the revenue has declined and the economic impact is yet to be known.
- What do you think the future looks like for the UK Rail industry and do you have any predictions of new equipment changes/ requirements in the years to come?
- I do believe the UK Rail industry is becoming more and more modernised and to keep up with that train manufactures and suppliers must keep updated with any new technology also how the process impacts the environment.
Our History with the Rail Industry
Our journey with the rail industry began in around 2005 when we started to work with Bombardier.
Our journey with the rail industry began in 2005 when we started to work with Bombardier, a relationship we have continued to this day. Over the years we have provided Bombardier with arrange of products which include jigs to aid in the manufacturing process, stillages for the safe transport of products and various stands, kitting media, and access platforms. Over the years we have nurtured relationships with various companies within the rail industry including Serco and Knorr-Bremse many of whom we still work closely with today and are active members of the the Rail Forum.

Case Study: To develop a methodology to store, transport and dispense electric and data cables for greatly improved handling and operational efficiencies.
A subsidiary of Bombardier, the train manufacturing company based in Derby provide prefabricated roof sections fitted with all the cabling requirements that supply power and data communications throughout the carriages and on to the engines.
This requires a diverse range of cables to be installed and tested in the roof section prior to being transported for final carriage assembly at Bombardier.
To achieve this, the roof sections are inverted and mounted on a gig. At one end of the section a crude steel framework is located into which spools of cable spools are located ready for an operative to draw the required lengths of cable along the roof section.
In order to load and unload the frame its spools requires the need for a steel bar to be inserted into the spool prior to it being lifted into position by two operatives.
Delays are being constantly experienced throughout the process as operatives capable of lifting the fully laden spools are sought out to perform the lifting and locating of the cable dispensers. Upwards of forty cable changes might take place during one shift.
Confronted with this most inefficient and time consuming process, the Company challenged Acres Engineering to develop a viable and functional methodology of efficiently and safely locating and dispensing any weight or size of cable spool by any operative at any time.
The engineering solution to overcome all the hurdles and pitfalls was very innovative and required a great deal of thought and experimentation from the outset by the engineering team at the Company.
The challenge to dispense with the manhandling of the spools was achieved by the development of a ramp wide enough to accommodate all sizes onto a platform. Wheeled into position and secured in place by the use of locking wheels, the spools could easily be rolled up the ramp by one operative. This novel solution created its own unforeseen engineering challenges and uncertainties as Acres Engineering attempted to advance this handling process from a standing start.
Settling on a five station carousel as the principle method of holding the spools, engineers sought to provide sufficient operational capacity and flexibility for the unit.
A solution of using steel draw bars onto which the cable spools could be located within each pair of carousel arms was developed and the draw bars could be located into pre-drilled holes along the length of arms to accommodate different diameters of spool.
The platform, frame and carousel could be loaded to dispense cable with relative ease, but it lacked any form of control over its method of rotation. This difficulty would be compounded as the spool weights in different locations within the carousel would alter as more and more cable was drawn from the spools during a working day.
Analysing the geometric variables of the spool configurations on the carousel, Acres engineers were challenged to devise a method to manage the variable weights during rotation via a crank handle operated by the Company personnel and also provide ease of use and safety for the operative.
Through their engineering expertise a gearbox seemed to be the only feasible potential solution. Experimentation took place to re-engineer and relocate the internal gear ratios to deliver a manageable rotation of the carousel by hand. At this stage operator safety was considered paramount especially considering the weight being rotated at any one time. The Company developed a robust and easily operated draw pin mechanism to lock and unlock the gear mechanism.
This novel solution has been a significant engineering achievement for the Company in greatly improving the ease, safety and efficiency with which the shop floor personnel can undertake the tasks of wiring roof sections of trains.