Duplex and Simplex Removal Machine for use with Waste Disposal Plant Gasifier
Duplex and Simplex Removal Machine for use with Waste Disposal Plant Gasifier
Duplex and Simplex removal machine withdraws and inserts Duplex and Simplex structures into and out of a Waste Disposal plant Gasifier unit. The serial number for this machine is: AD-974-2016-02 . The Duplex and Simplex removal machine is a fully…
Read More
Duplex and Simplex removal machine withdraws and inserts Duplex and Simplex structures into and out of a Waste Disposal plant Gasifier unit.
The serial number for this machine is: AD-974-2016-02 .
The Duplex and Simplex removal machine is a fully certified and CE marked solution. The machine consists of:
1x Header Unit Trolley
1x Trailing Trolley A
1x Trailing Trolley B
Duplex Push+Pull Tool
Simplex Push+Pull Tool
Chain Set
2 x Powered Tug units
The solution offered by Acres Engineering avoids the use of a winch or block and tackle which could potentially be assessed as high risk and required ongoing certification (LOLER). By pulling at the front of the solution there is less force required throughout the whole structure enabling us to offer a reduction in product weight and cost.
The specified Rams have a 100mm bore, 50mm rod (EN8 grade steel), 1500mm stroke, pressure rating up to 200 Bar and an operating speed of up to 0.5m per second.
Our offered solution for the Duplex/ Simplex Removal and Insertion Trolley ‘DSRIT’ comprises of four individual modules bolted together. Three of the modules are referred to as ‘Trailing Trolleys’ and the one of the trolleys, the removal trolley is referred to as the ‘header trolley’.
The header trolley has been designed to be a single device capable of removing both the simplex and duplex feeders from the combustion chambers.
It has been designed this way to increase flexibility and reduce manufacturing/ transport costs. Each unit is 5m long giving a total length of 20m. We believe our core product offers a robust solution for the challenge and is complemented by a number of additional options to make the operation safer and more efficient.
Enquire now and add a Hone 2000 to your manufacturing capability: Talk to us today: [email protected] / 01332695240 / Contact Us Form
Please note: We can offer smaller or larger footprints with customised functionality.
Salient Points:
· The acronym DSRT will be used for Duplex/Simplex Removal Trolley throughout this manual
· The DSRT is to be used with a pre-approved gasifier unit only.
· Before using the DSRT, follow the safety instructions in this manual.
· DSRT operators must be authorised, trained and familiar with the machine.
· During operation there should be no personnel within 1 metre distance of the DSRT.
· When moving the carriage, always select direction first and control the DSRT with the handheld controller.
· The hydraulic power unit needs a rest time between usage. It is not designed for continuous use.
· The DSRT is designed to move the Duplex/Simplex across nylon slides, not metal to metal..
Specificaiton:
Weight: 7300kg unladen
Voltage:400/50/3PH
Power: 4kw
Pressure: 200 bar
Hydraulic Specification:
5.5Kw electric motor close coupled to fixed displacement gear pump to give 15 LPM / 200 Bar. Vertically mounted with the pump submerged on a 100L steel reservoir furnished with filler breather, oil sight level gauge with temperature scale and 10 Micron return line filter.
Directional control valves will be mounted on two station manifold with integral relief cartridge to control 2x pull cylinders (150mm bore, 90mm rod & 1500mm or 2000mm stroke).
If limit switches are not reached within a set time (yet to be advised) during any of the process then the pack will shut down and a visual warning light will indicate a problem.
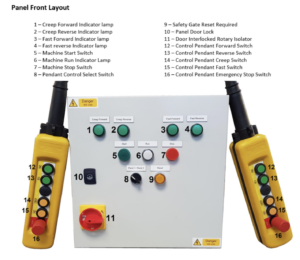
Structure Design:
The main structure is manufactured from 60mm x 60mm x 5mm box section, heavy duty channel and 12mm plate. The fabrication will be tacked welded and then the frame will be stitch or fully welded. Certificate of welders weld test will be supplied. The welds will not be tested apart from a load test (no NDT etc).
A single castor will be supplied to confirm agreement from flooring contractor before continuing to procure the additional 15 castors. Alternative castors may lead to additional costs.
We have selected a 200mm diameter castor with a 1200kg load rating from one of the best manufacturer in the industry, Bickle. The castor is a Welded steel heavy duty castors with steel spring, wheel with Blickle Softhane® polyurethane tread. Bickle Softhane are heavy duty castors and wheels made of green, reaction-injected polyurethane-elastomer in 75° shore A hardness. The thick, elastic Blickle Softhane® tread ensures very high operational comfort.
What is a Waste Disposal Plant Gasifier?
A Waste Disposal Plant Gasifier is a facility designed to convert waste materials into gas through a process called gasification. Gasification is a thermal process that transforms organic or fossil-based carbonaceous materials into carbon monoxide, hydrogen, and carbon dioxide, under a controlled amount of oxygen and/or steam. This process is different from incineration, which burns the waste completely to ash.
The gas produced, commonly known as syngas (synthetic gas), can be used as a fuel to generate electricity or as a basic chemical feedstock in the chemical industry. The process significantly reduces the volume of waste, helps in managing waste disposal, and produces valuable byproducts, thereby offering an environmentally friendly alternative to traditional waste disposal methods like landfilling and incineration.
The key components of a Waste Disposal Plant Gasifier include:
- Feedstock Preparation: Waste materials are prepared for gasification, which may involve sorting, shredding, and drying to ensure consistent feedstock quality.
- Gasification Chamber: The prepared waste is fed into the gasification chamber, where it is heated at high temperatures in a low-oxygen environment. This process breaks down the molecular bonds in the waste material, producing syngas.
- Syngas Cleanup and Treatment: The produced syngas contains impurities such as tar, ash, and particulate matter. It undergoes a cleanup process to remove these impurities, making it suitable for use.
- Energy Recovery: The clean syngas can be used in various ways, including generating electricity, producing heat, or as a feedstock for producing chemicals.
- Ash Disposal: The inorganic components of the waste (not converted to syngas) are left as ash, which can sometimes be used in construction materials or needs to be disposed of safely.
Waste Disposal Plant Gasifiers offer several advantages, including reducing the amount of waste going to landfills, producing energy from waste, and potentially reducing greenhouse gas emissions compared to direct combustion processes. However, the technology and infrastructure require significant investment, and the economic viability can depend on the specific characteristics of the waste stream, energy prices, and regulatory environment.
Several companies around the world specialize in the development and manufacture of gasification technology and equipment. These companies offer a range of solutions tailored to different types of feedstocks, including municipal solid waste, biomass, industrial waste, and coal. Here’s a list of some notable companies in the field:
- Covanta: Covanta is a leader in providing sustainable waste and energy solutions, including waste-to-energy gasification technologies. They focus on converting municipal and industrial waste into renewable energy.
- Enerkem: Enerkem develops technology for converting municipal solid waste into biofuels and renewable chemicals through gasification. Their technology is known for processing diverse types of waste materials.
- Siemens Energy: Siemens Energy offers gasification technology solutions for various applications, including power generation and the production of chemicals. They focus on high-efficiency, low-emission gasification processes.
- Thermoselect: Specializing in high-temperature gasification technology, Thermoselect offers solutions for converting waste into energy and valuable products, emphasizing environmental benefits and efficiency.
- Alter NRG/Westinghouse Plasma: Alter NRG, through its Westinghouse Plasma technology, provides plasma gasification systems that convert waste into syngas for energy production. Their technology is suitable for a wide range of waste types.
- Outotec (now part of Metso Outotec): Known for their expertise in metals and mining, Outotec also offers solutions for energy production, including gasification technology for biomass and waste-to-energy projects.
- Babcock & Wilcox Volund: Babcock & Wilcox Volund offers advanced waste-to-energy technologies, including gasification solutions for turning waste and biomass into energy and heat.
- GE Power: GE Power provides gasification technology that can process a variety of feedstocks, including coal, biomass, and municipal solid waste, for power generation and chemical production.
- EQTEC: Specializing in advanced gasification technology, EQTEC offers solutions for converting biomass and waste into clean energy. Their technology emphasizes sustainability and efficiency.
- SynTech Bioenergy: Focused on renewable energy, SynTech Bioenergy provides biomass gasification technology that converts waste into clean, renewable energy.
These companies are at the forefront of developing and deploying gasification technologies, contributing to the advancement of waste-to-energy solutions globally. Each company has its specific areas of expertise, types of gasification technology, and target markets, making them leaders in the field of waste gasification and sustainable energy solutions.
Who Operates Waste Disposal Gasifier Plants?
Acres design and manufacture lots of different machines.
We also manufacture access platforms, jigs and fixtures and many other types of product.
Talk to us today about your requirements: [email protected] / 01332695240 / Contact Us Form
Want to know more about Acres Engineering?
Check out our latest blog posts.
We post about our support of the Armed Forces, STEM and Charity.
We offer a range of information guides.
We make it easy to engage with us, we are approved on: JOSCAR / AVETTA / COUPA / SAP ARIBA / DEEPSTREAM….you can download our BSI / Insurance certificates here.
Have a design and development project you want the Acres team to look at? Can’t see what you want? Need something different?
Acres Engineering is established as a leader in delivering bespoke creative engineered solutions. Many OEM’s and tier one/ two suppliers in aerospace, automotive, rail and power generation industries have chosen us as their solutions partner because of our innovative attitude towards individual challenges and commitment to continual improvement.